Assessment and Evaluation of Friction Welds
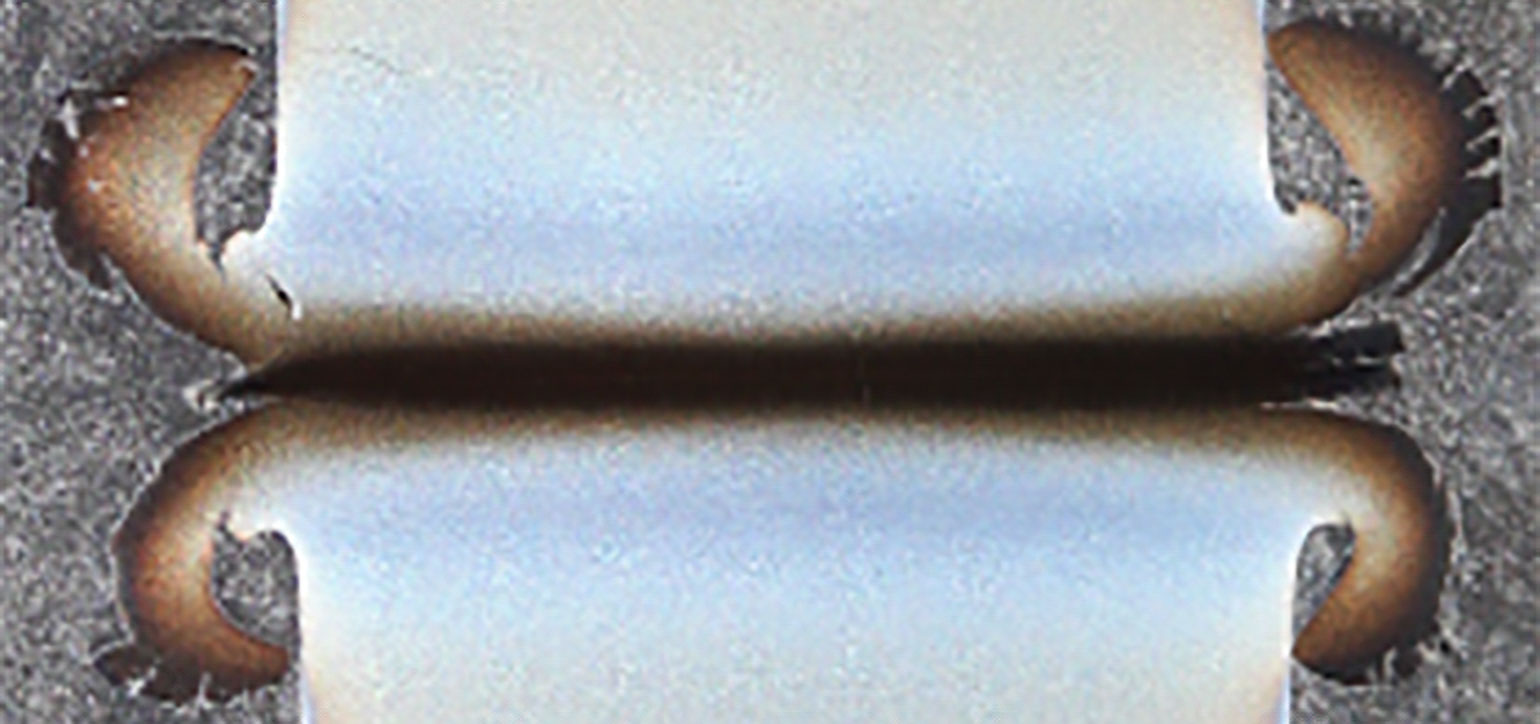
20 Oct 2020
How can you join complex components together?
Friction welding is a popular solid-state joining technique used in industries which require joining similar and dissimilar materials. The most common processes are:
- Inertia friction welding (IFW)
- Linear friction welding (LFW)
- Rotary friction welding (RFW)
- Friction stir welding (FSW)
- Friction stir spot welding (FSSW)
The successful commercialisation of friction welding and its significance in welding are due to the following benefits:
- No consumables are involved
- Materials remain in the solid-state
- Less distortion
- Automated process
- Easy to join up complex parts
- Joining of dissimilar materials that have been previously un-weldable
Typically, the workpieces are joined by friction motion which generates heat and mixing. For processes such as RFW, IFW and LFW, "flash" is extruded as a result of the rubbing motion from two workpieces. There is a need for standardising the friction welding processes, especially for safety critical products and quality improvements.
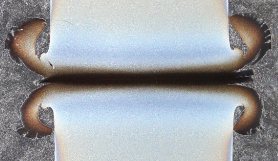
Due to the nature of solid-state joining, defects associated with fusion welding are eliminated. However, other types of anomalies arise within the heat affected zone (HAZ). The "flash" expelled from the friction welding process can reveal essential information about the welding process. Oxides, porosity, foreign particles, cracks can often be found in the flash, which are indicative of the suitability of welding parameters used.
What can Intertek do for you?
As specialists, we can complete assessments of welds and flash. Our services include
- Deconstructing specimens
- Metallurgical preparation of samples
- Assessment for microstructural defects in your weld
We use a range of destructive and non-destructive techniques such as:
- Three-point bend tests
- Visual inspection
- Optical microscopy
- Scanning electron microscopy (SEM)
- Energy-dispersive X-ray spectroscopy (EDS)
- Hardness testing
- Complimentary tests such as tensile and corrosion tests can reveal additional information
Altogether, these tests can help to ensure an integral weld is produced. Further, investing in quality assurance and continuous improvement in manufacturing can help to drive costs down in the long-term.
Combined with information and parameters gathered during friction welding, analysis and results can be built into a database to improve the lifecycle management of your product. Learn more about friction weld analysis and understand more about the range of testing we offer.
https://www.intertek.com/non-destructive-testing/welding-services/
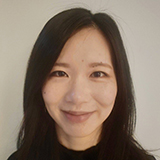
Helen Liu,
Team Leader (Friction Welding)
Helen is a Team Leader in Derby, UK. She joined Intertek in 2013 after leaving Imperial College London and has previously worked for General Electric. She is currently in the Young Members Committee for The Welding Institute and is also a member of Institute of Materials, Minerals and Mining (IOM3).